The four main techniques
Types of Welding
What are the different types of welding techniques?
There are four main types of welding processes typically used in Australia to weld metal. Commonly known as MIG, TIG, Stick and Flux-Cored, each has it’s place in the trade. Selecting the right welding process can depend on the metals being used, the application, the location and the required look of the resulting weld.
Each of the below techniques involves 4 key components – the base metal, the filler metal, a heat source (in this case electrode and electrical arc) and shielding from atmospheric contamination (via an external gas or flux).
In general terms, the process works like this; the electrode causes an electrical arc, which heats the base and metal fillers to heats causing them to melt. The resulting metal puddle, or welding pool, joins together before resolidifying (creating the weld). Importantly, during this process, a shielding gas covers the weld pool, preventing exposure to oxygen, nitrogen and hydrogen contained in the air atmosphere. Such exposure can affect the integrity of the weld. In addition, shielding gas influences weld penetration, arc stability and the mechanical properties of the finished weld.
MIG – Gas Metal Arc Welding (GMAW)
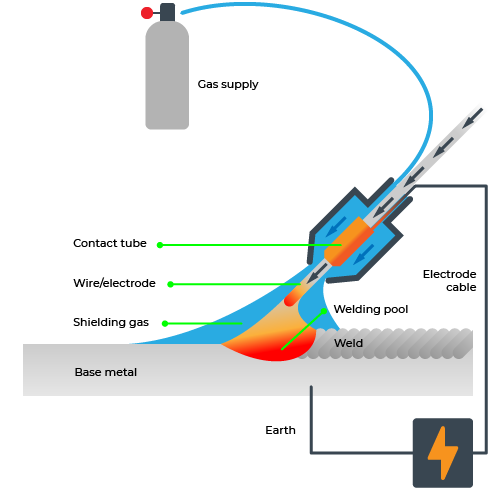
One of the most common types, MIG Welding uses a continuous (and sacrificial) wire that acts as both the electrode and the filler metal. Fed off a spool, and through the welding gun, the wire can be fed at a speed that suits the welder and the application. The welding gun itself expels the inert shielding gas, typically argon, to protect the weld from contaminants in the air.
MIG welding is a simple form of welding and is compatible with many different metals and thicknesses.
TIG – Gas Tungsten Arc Welding (GTAW)
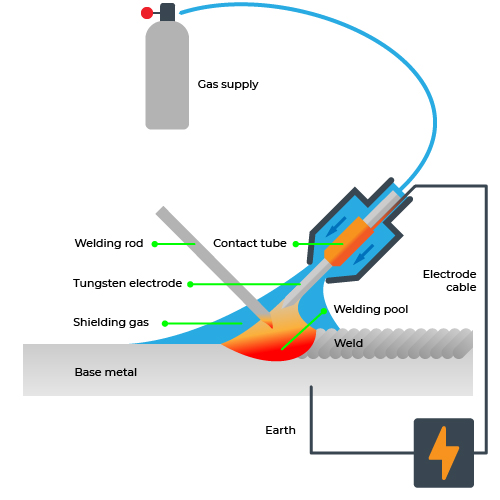
TIG welding uses an electrode made of tungsten. As one of the toughest metals, the tungsten electrode will not dissolve (non-sacrificial) – and is therefore not used as the filler metal. Without the need for a filler metal, the TIG welding process can perform what’s known as fusion, combining two base metals, although introduced fillers can be used. Again, an external shielding gas is used via the welding gun.
TIG welding is often used on thin stainless steel sections, and non-ferrous metals such as aluminium and copper alloys.
Stick – Shield Metal Arc Welding (SMAW)
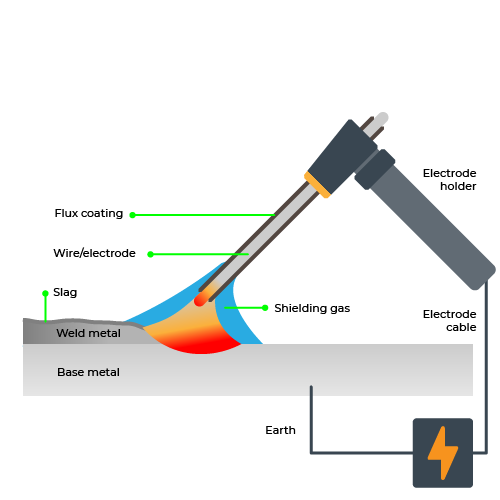
Stick welding is perhaps the simplest form of welding. The name ‘stick’ is derived from the component used in this process that provides both the electrode and the filler metal. In addition, this replaceable electrode stick is coated in flux, that when heated creates a gas cloud protecting the weld zone from atmospheric contamination. This also means that Stick welding does not require an external gas source.
Although a simpler process, quality stick welding can require a high skill level.
Flux Cored Arc Welding (FCAW)
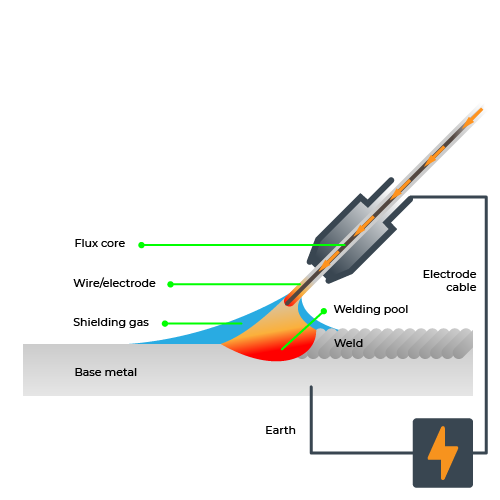
FCAW is similar to MIG welding, in that it also uses a continuous wire that is fed through the weld gun, and serves as the electrode, and the filler metal. Unlike the MIG wire, FCAW wire has a flux core that when heated creates the gas shield. The flux core, in most instances, eliminates the need for an external gas supply.
Often used on thicker, heavier metals, FCAW is ideal for heavy equipment repairs, however, will not result in the cleanest weld and may require clean up.